Dispenser, also known as glue applicator, glue dispenser, glue dispenser, etc., is an automatic machine that specially controls the fluid, and dispenses and coats the fluid on the surface of the product or inside the product. The glue dispenser is mainly used for the precise point, injection, coating and dripping of glue, paint and other liquids in the product process to the precise position of each product, which can be used to achieve dots, lines, circles or arcs.
Dispensing principle analysis
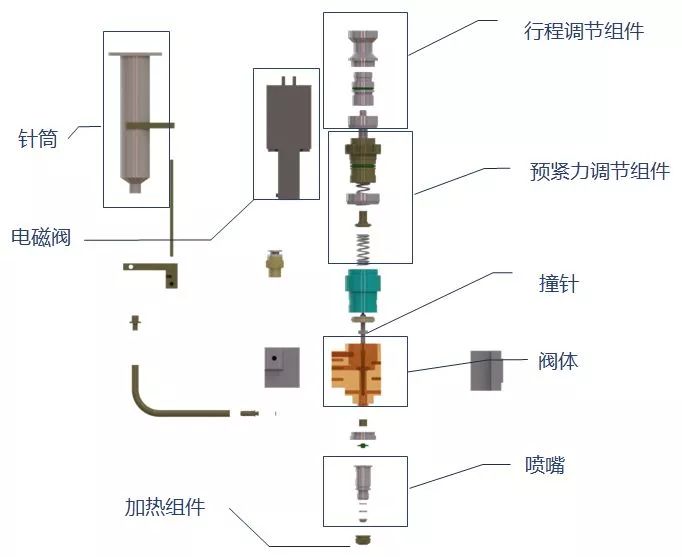
Valve body exploded view
The fluid fills the cavity channel under the action of the feed pressure.
Open the solenoid valve, the compressed air enters the valve body, pushes the striker assembly to move upward until it contacts the lower end of the stroke adjustment rod, and the striker assembly rises by a distance h (Note: h is an adjustable variable, controlled by the stroke adjustment assembly); and stay at this position For an appropriate period of time, the striker pin separates from the nozzle pad and fluid enters the nozzle striker seat.
When the solenoid valve is closed, under the action of the pre-tightening force, the striker quickly hits the nozzle and strikes the seat, and the pre-pressure potential energy of the spring is converted into the kinetic energy of the downward movement of the striker assembly. Glue droplets are sprayed out through the nozzle.
Industry application
1. Underfill
2. Surface Mounted Package (Surface Mounted Package)
3. PCB board (Coating)
4. Component & Chip Pin Encapsulation

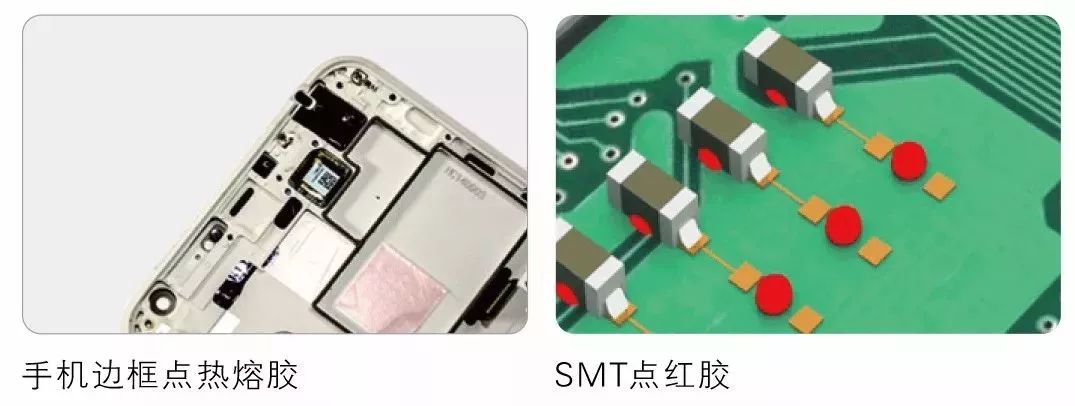
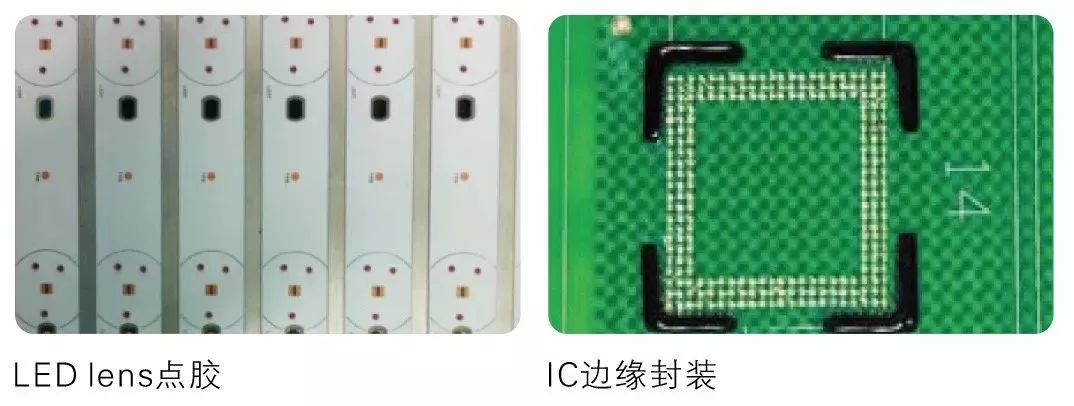
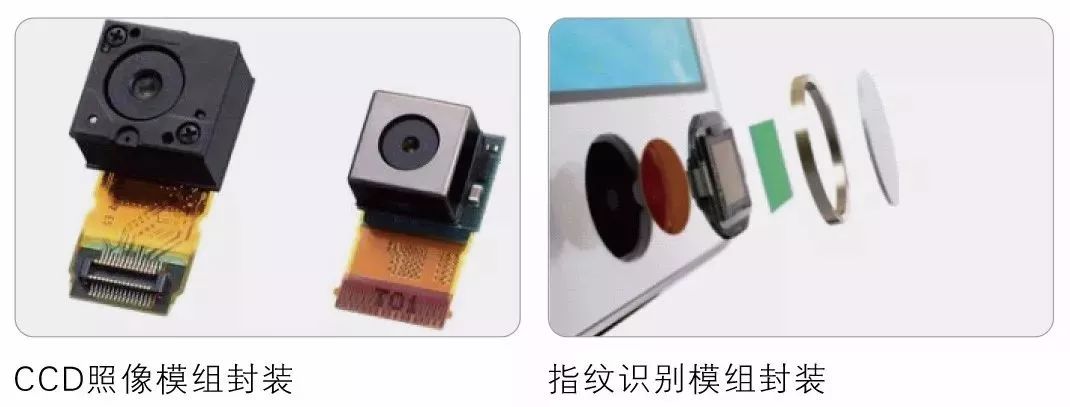
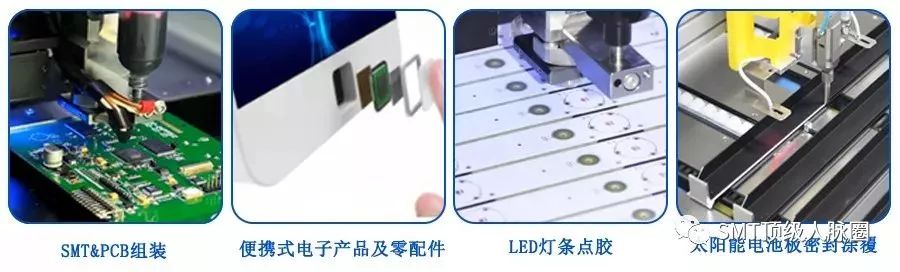
Factors for precise glue control
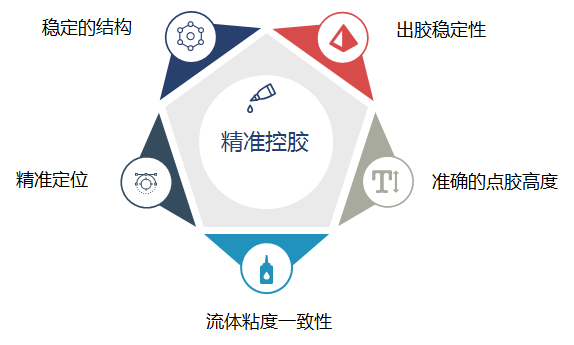
Commonly applicable liquid glues
Various solvents, adhesives, paints, chemical materials, solid glues, etc., including silicone, EMI conductive glue, UV glue, AB glue, quick-drying glue, epoxy glue, sealant, hot glue, grease, silver glue , red glue, solder paste, thermal paste, solder mask, clear paint, screw fixer, woodworking glue, anaerobic glue, acrylic glue, anti-abrasion glue, crystal glue, pouring glue, speaker glue, instant glue, rubber, paint , enamel paint, lacquer, ink, pigment, etc.
As a kind of automatic glue dispensing equipment, automatic dispensing machine is widely used in electronic smart phone industry, lighting industry, automobile industry, industrial electrical, solar photovoltaic and other industries. The most common problem encountered by the automatic glue dispenser is the valve problem. The following are effective methods to solve the problems that often occur when the glue valve is used:
1. The nozzle is blocked
Reason: The pinhole of the automatic glue dispenser is not completely cleaned, the patch glue is mixed with impurities, there is a hole blocking phenomenon, and the incompatible glue is mixed, resulting in a small amount of glue nozzle or no glue point.
Solution: change the clean needle, change the patch glue with better quality, and the grade of the patch glue should not be mistaken.
2. Valve dripping
Reason: The diameter of the needle used in the glue dispenser is too small. If the needle is too small, it will affect the bubble removal action of the valve when it starts to use, which will affect the flow of the liquid and cause back pressure, resulting in the phenomenon of dripping soon after the valve is closed.
Solution: This problem can be solved by simply replacing the larger needle. In addition, the air in the liquid will leak after the valve is closed. It is best to remove the air in the liquid in advance, or use a glue that is not easy to contain air bubbles, or use the glue after centrifuging and defoaming.
3. The flow rate is too slow
Reason: The pipeline of the glue dispenser is too long or too narrow, the air pressure of the nozzle is insufficient, and the flow rate of the glue is too slow.
Solution: Change the pipeline of the dispenser from 1/4' to 3/8', and the pipeline should be as short as possible if not needed. In addition, the glue port and air pressure should be improved, so that the flow rate can be accelerated.
4. There are air bubbles in the fluid
Reason: Due to excessive fluid pressure and short valve opening time, the dispenser may infiltrate air into the liquid, resulting in the generation of air bubbles.
Solution: Reduce fluid pressure and use tapered, beveled needle.
5. The glue size is inconsistent
Reason: The pressure cylinder or air pressure of the fluid stored in the dispenser is unstable, resulting in uneven glue output and inconsistent size.
Solution: Avoid using the low pressure part of the pressure gauge. The control pressure of the glue valve should be at least 60psi to ensure stable glue output. Finally, the glue dispensing time should be checked. If it is less than 15/1000 seconds, the glue dispensing will be unstable. The longer the glue dispensing time, the more stable the glue dispensing.
How does the automatic glue dispenser solve the drawing when using glue with higher viscosity?
Under normal circumstances, low-viscosity glues are mostly used for large-area application, such as laminating, potting, large-area bonding, etc. Medium-viscosity glues are easy to operate, suitable for most bonding, sealing and other operations, high-viscosity glues It is difficult to spit out, and the fluidity is weak or almost no fluidity. It is suitable for cofferdam, reinforcement, etc. Due to the needs of the process, some products must use glue with a higher viscosity. During the dispensing process, due to the high viscosity, sometimes it will be drawn, which affects the quality of the dispensing and the aesthetics. So how to solve the drawing?
complete solution
If the company has very strict requirements on product quality, it can be considered from the hardware aspect. The dispensing valve is equipped with a valve specially designed for high-viscosity fluids, such as an imported screw valve, and the glue viscosity value is provided to the manufacturer, and the manufacturer will target the glue. The viscosity value , to help you match the type and achieve the perfect dispensing effect. Of course, for the high-viscosity screw valve, the price will be more expensive, but it can help you solve the drawing phenomenon perfectly.
Other solutions
1. Glue opening delay
When opening the glue head, because there is a distance between the glue head outlet and the glue valve, there is no glue between this section. If you open the glue head output port and start moving immediately, it will cause a short section of the track to lack glue. To prevent this, after the glue is opened, delay for a period of time, wait for the glue to flow out, and then perform subsequent movements. This delay time is called the glue opening delay.
2. Glue off delay
After closing the glue head, there is still glue between the glue head and the glue valve. If the glue head moves immediately after closing the glue head, it may cause glue tailing. In order to prevent this, after closing the glue head, delay for a period of time to wait for the glue to flow out, and then perform subsequent actions. This delay time is called glue off delay.
3. Drawing height
Due to the high viscosity of some glues, the glue wire can be broken by slowly lifting it up at a constant speed for a certain distance without affecting the glue application trajectory. This distance is called the wire drawing height.
4. Lift height
After the dispensing of one track is completed, when the rubber head is moved to the starting point of the next track, in order to prevent the rubber head from hitting the needle, lift the rubber head up a certain height at the end point to ensure the safety of the rubber head without hitting the needle, and then idly move to the starting point of the next track. The starting point, this height is called the lift height.
5. Close the glue in advance
'Close glue in advance' is the distance of glue close in advance, which means that in the continuous track gluing, close the glue head before reaching the end point, and use the residual pressure and residual glue to complete the last section of the track, so as to avoid the end section of glue. The length is the 'gluing distance'.
6. End the action
After the dispensing of the entire teaching track is completed, in order to facilitate picking and placing workpieces, improve processing efficiency or eliminate processing errors, the user can set the glue head to move to the specified position, or the starting point of the processing file, or the end point of the processing file, or reset, or Make file connection. This project is called the end action.
7. Incline Pull Up
Due to the viscosity of the glue, the wire drawing action directly after closing the glue cannot achieve the effect of breaking the glue wire, or the shape of the pulled glue wire does not meet the requirements. Therefore, after closing the rubber head, perform a diagonal pull-up action to prepare for wire drawing.
8. Glue heating
You can try to heat the glue to a suitable temperature to increase the fluidity of the glue, and it can also solve the drawing in a sense. (Be careful not to heat too high!)
Influence of dispensing height on precise glue control
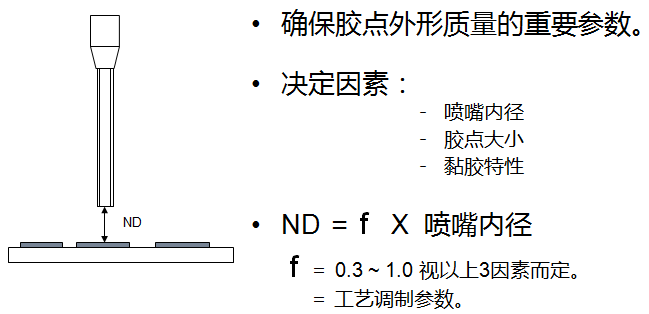
I believe everyone knows the above common fault causes and solutions of automatic glue dispensers. These common problems can be big or small, and users can quickly solve them as long as they master the correct solutions.
Esight Techonology focuses on industrial vision intelligent technology. It has accumulated ten years of technology and five years of process polishing to create the most professional industrial vision precision dispensing system. If you have any special process requirements for dispensing, please contact us at 0755-23605463 (info@esightech.com.cn).