As smartphones become more widely used and more convenient, their structures are also more complex, including connectors, touch screens, metal shells and glass covers, FPC flexible printed circuit boards, PCB motherboards, cameras, batteries, Cover, antenna, bottom cover, as well as chargers, headphones, etc.
In the pure manual production line, the quality control personnel in the mobile phone motherboard production workshop will pick up the magnifying glass to check the accuracy of the materials loaded by the workers for the high-speed placement machine, and mark the motherboard. Mainboard production is the first step in the production of mobile phones in addition to material procurement.
Next, the screen of the mobile phone to be assembled and the camera of the mobile phone are installed in place. Then the workers began to test the phone's calling function, camera function, etc., charging the phone and testing the battery performance.
After each function is running normally, scan the IMEI serial number (International Mobile Equipment Identification), which is the last link in the assembly of the entire mobile phone. After the mobile phone passes the test in the assembly test area, it enters the packaging process. The workers pack the accessories and product manuals of the mobile phone, and finally pack them for inspection.
■ The current state of automation in the smartphone production chain
Divided according to the process, the mobile phone industry chain can be divided into assembly section, core component section, and testing section.
The assembly section includes dispensing, precision placement, pre-assembly, as well as precision pressing and screw locking. These automated equipment have basically achieved mass production.
The core component segment includes SMT, PSA, laser cutting, marking, welding, as well as automatic loading and unloading, polishing, grinding, engraving, hot bending and other equipment, and a relatively small module such as a camera needs to be assembled.
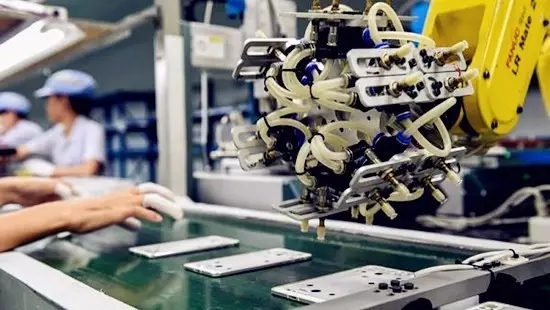
Inspection section, including dimension measurement, such as flatness, level difference, gap, and defect inspection; also includes performance inspection, such as RF, audio, MMI, etc., these performances can be detected by special instruments.
When the various components of the mobile phone are assembled and the back cover of the mobile phone is fastened, the assembly of the mobile phone tends to be completed. After the mobile phone is assembled, specific items such as audio, photography, GPS, antenna, and functional testing are also tested.
At present, robots can assist in automated inspection of assembled products, including audio, photography, GPS, antenna, functional testing and other items. According to mobile phone manufacturers, the accuracy of robot inspection can reach 98%. In addition, fixed actions such as moving mobile phones and positioning detection during the inspection process can also be replaced by robots, which can reduce at least 20 manpower in each production area.
In the test of the whole machine, a robotic arm, a large-scale automatic detector, an AOI automatic optical detector, etc. are used. Through the man-machine interface, the SIM card detection, battery test, SD card detection, LED button, LCD test, LED backlight, etc. of the mobile phone can be tested All parts of the phone are tested.
Overall, SMT is the most automated process and the most popular electronic assembly technology today. First, the printed circuit board (PCB) is printed, and then the chips such as the processor are pasted on the PCB with solder paste, and the temperature is fixed. Through computer monitoring, it is possible to observe whether the printed circuit board is defective and mark it. After the main board is fully fabricated, it will be sent to the mobile phone pre-assembly production line for production. The entire process can now be fully automated.
The manpower-intensive area is mainly concentrated in the assembly of the whole machine, including assembly, testing, packaging, etc., because it involves welding, cycloid, closing the shell, cleaning the display screen, attaching lenses, testing and testing, as well as the feeding and lamination of accessories, etc. Process, automation transformation is more difficult, coupled with the production characteristics of small batches and multiple batches, which puts forward higher requirements for the flexibility of automation.
Relatively speaking, the packaging process in the latter stage is less difficult, and there are already relatively mature cases. An automatic packaging machine can be configured on the production line to replace the original manual packaging, which can realize the packaging automation of the entire line.
In addition to the production process, the factory has begun to equip AGVs in the transportation process. According to Wang Maolin, a partner of Stand Robotics, the value of AGVs lies in the high degree of flexibility in handling materials from raw material warehouses to production lines and then to finished product warehouses. , It is necessary to achieve rapid deployment without changing the original production line, and form a flexible production line, so as to realize AGV replacement of 'people' and 'magnetic strip cars'.
■ Automation of mobile phone production lines has become a trend
Data shows that 70% of the world's electronic products are manufactured in China, but in the entire production process, 90% of the processes are still dominated by manual operations, which means that there is huge room for intelligent transformation in the future.
Mobile phone process and automation transformation space
First of all, in the previous process, that is, the processing of shell materials, plastic materials, metal materials, etc., such as CNC processing of the middle frame, can be realized by polishing and grinding process. In addition, in the process of card slot, HOME button size detection, spraying, PCB board assembly and testing, etc., automation integrators who are deeply involved in the mobile phone industry chain can design automation transformation solutions.
Secondly, in mobile phone manufacturers or foundries, the assembly and testing process accounts for about 80% of the labor flow of the entire industry chain. 'Machine substitution' has both difficulties and opportunities.
Liao Shenghua, general manager of Cooper Robotics System Department, introduced that through the intelligent force-controlled flexible assembly solution and human-machine collaboration AI intelligent production line solution, the AI visual inspection platform can be applied to robots disorderly loading and unloading, intelligent force-controlled flexible assembly , Robot force-controlled grinding, intelligent defect detection.
The last step is the back-end packaging. After the finished product passes the MMI test and the QR code is written, it will enter the packaging, packing and palletizing and other links. This is also a relatively mature field for domestic industrial robot manufacturers.
According to industry estimates, in the four major links of pre-process, assembly, testing and post-packaging, the pre-process may account for 10% of the employees, 60% for assembly, 20% for testing, and 10% for packaging. According to the distribution of this labor force, from the perspective of reducing staff and increasing efficiency, there is a large space for automation and upgrading of assembly and testing.
■ New requirements for mobile phone automated production lines
At present, there is still a big contradiction between the increasingly urgent automation needs of mobile phone manufacturers and the capabilities of automation manufacturers.
First of all, mobile phone products are small batches, multi-variety, high process complexity, and require fast beat speed, so high flexible production lines are required to be compatible with all its series of products.
In addition, the life cycle of single-model products is getting shorter and shorter, and the upgrading of new functions such as OLED full display, hyperboloid glass, wireless charging, facial recognition, 3D camera, and 5G is accompanied by technological innovation.
Second, the depreciation cycle of equipment needs to be taken into account. At present, the service life of equipment is about 3 to 5 years, while the production cycle of mobile phones is relatively short, about 8-12 months, so the reusability of equipment is required to be high.
Third, it is strict with the investment return period, and end customers require that the cost can be recovered within one and a half to two years.
From the perspective of end users, the introduction of production lines by medium and large enterprises mainly considers whether they are suitable for the development of Industry 4.0. Large manufacturers have the support of large orders and hope to upgrade the automation of the entire line to improve their market competitiveness.
Therefore, medium and large-scale terminal enterprises need internal + external cooperation, and the implementation of hardware + software will test the plasticity and decisiveness of the enterprise itself, because a lot of money needs to be invested.
For small and medium-sized enterprises, cost is the first factor to be considered, and the return on investment period is also considered. At present, small and medium-sized enterprises are mainly manual or semi-automated, and they are more inclined to replace single-station automation, from manual to semi-automatic and automated upgrade iterations.
From the perspective of system integrators, larger integrators should integrate from production lines, logistics to systems, strengthen investment in software development, data interpretation, interface processing, etc., and develop towards digital factories.
Small-scale integrators should specialize in a certain field, and actively cooperate with robot manufacturers in specialized and customized cooperation. Cooperation is a better path.
From the perspective of the body manufacturer, according to the characteristics of the 3C industry, firstly, the robot needs to be able to adapt to flexible production, quickly complete the preparation for product production, and meet the differentiated needs of users; secondly, the robot needs high precision, high speed, or It has 'one skill' in some indicators; third, robots tend to be miniaturized and lightweight, which saves space and facilitates users to modify existing products.
Lu Zhangyuan, director of the Robotics Research Institute of the High-tech Industrial Research Institute, said that, in fact, application solutions and project implementation are the keys to success. Ontology manufacturers, distributors and integrators work together to develop application solutions for specific process segments and create the goal of standard process segment applications. It can be reproducible, high reliability, fast introduction, and the return on investment period is less than 1 year.
Therefore, robot body manufacturers and system integrators need to cooperate sincerely with end customers and automation enterprise customers to jointly develop mobile phone intelligent production lines and make mobile phone enterprises intelligent in production.
【reprint】High-tech robot